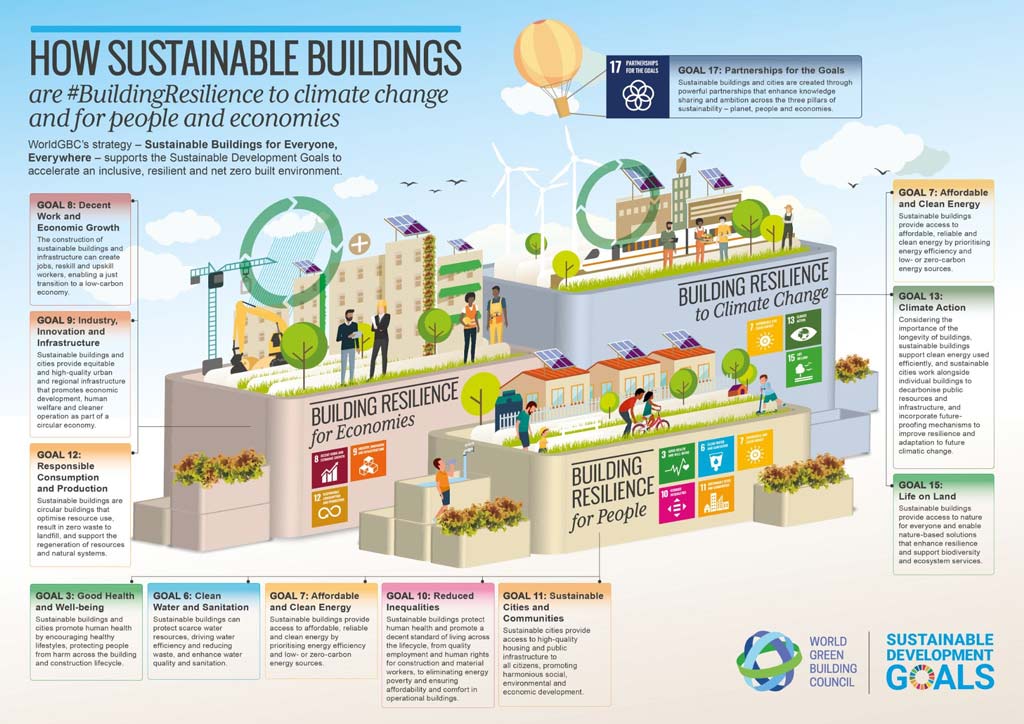
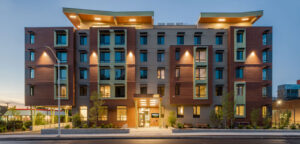
“While each region of the U.S. faces a unique combination of weather hazards, every state in the country has been impacted by at least one billion-dollar disaster event since 1980,” says Adam Smith, an applied climatologist with the National Oceanic and Atmospheric Administration (NOAA) in Ashville, N.C., who tracks extreme weather events that cause more than $1 billion in damage.
“Over the last four decades (1980-2019), the U.S. has sustained 250 separate weather and climate disasters where overall damages/costs exceeded $1 billion (including Consumer Price Index adjustment to 2019). The total cost of these 250 events exceeds $1.7 trillion,” he adds. “The concrete industry has a huge opportunity to not only offer a solution to this devastation with more resilient homes and buildings but also to save lives.
Climate Change
The extreme weather events that are increasing as a result—have spurred a new debate in regards to constructing homes and buildings with concrete versus wood. While we have been buildings homes with light-frame wood construction since the 1950s, a need for more resilient construction is growing.
“While each region of the U.S. faces a unique combination of weather hazards, every state in the country has been impacted by at least one billion-dollar disaster event since 1980,” says Adam Smith, an applied climatologist with the National Oceanic and Atmospheric Administration (NOAA) in Ashville, N.C., who tracks extreme weather events that cause more than $1 billion in damage.
“Over the last four decades (1980-2019), the U.S. has sustained 250 separate weather and climate disasters where overall damages/costs exceeded $1 billion (including Consumer Price Index adjustment to 2019). The total cost of these 250 events exceeds $1.7 trillion,” he adds.
The concrete industry has a huge opportunity to not only offer a solution to this devastation with more resilient homes and buildings but also to save lives.
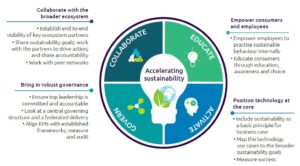
Sustainability Gains Traction
The demand for a green environment and sustainability will continue to evolve this year within the industry. The cement industry, which is a major component in concrete, unfortunately, seems to get a black eye in terms of sustainability—something Poston says is “probably unjustifiable in some ways.”
“It certainly takes a lot of energy to produce cement, but when you look at the other side of the equation and look at the resiliency of concrete and its durability, you get a much longer life out of a concrete structure,” he notes.
Phillips agrees, adding that “correcting the false narrative” is at the top of the NRMCA’s to-do list in 2020.
“We have a tremendous story to tell from a concrete perspective on the contributions we’ve made to society, to human health, to life safety to resilient communities, and that’s all wrapped in being able to tell a very truthful and fact-based narrative about the impacts of concrete in these carbon discussions that we’re having,” he says.
Combined the cement and concrete industries are the second-largest industrial emitters of CO2 on the planet, accounting for about 8% of global CO2 emissions. Phillips suggests, however, that concrete’s natural ability to absorb atmospheric carbon will allow the industry over time to be part of climate change solutions.
A 2016 paper in Nature Geoscience supports this claim, suggesting that the world’s concrete has been absorbing about 43% of those original emissions. There may be some ways to speed up or strengthen this absorption process, which is an area that scientists are still working on.
In the meantime, the NRMCA is working on engaging its members and producers throughout the industry to take an interest in the topic. “This is an issue that needs full engagement from our members and other producers,” Phillips adds.
And while blaming the world’s environmental woes on the concrete industry is far from fair, there will continue to be interested in alternative options for sustainable building.
“It’s not coming from all directions, but I can feel an upsurge and the need for that,” Poston says, pointing specifically to long-term investors or property owners and public agencies.
In preparing for that upsurge, ACI updated its most recent building code from ACI 318 19 to include provisions that allow for recycled aggregates and alternative cement that doesn’t have as much portland cement. It is the first time using alternatives that have been codified.
“We’ve given the nod to those that are acceptable, but they have to demonstrate certain performance requirements before they are utilized on a project,” Poston notes.
Technology Keeps Advancing
The use of technology to make life easier, more efficient and profitable for the contractor will continue to trend. “ACI, for example, has plans to roll out an interactive building code called 318 Plus that will make it easier to keep up with ever-changing codes. There’s this feeling from designers that we’re getting more and more codes and they’re changing all the time. How do we keep up with all this,” Poston says.
In addition to a reorganization of the codes, this program will allow you to look at diagrams in 3D.
“Everybody thinks that, unfortunately, the concrete industry doesn’t adapt that well to those sorts of things,” Poston notes. “But now more than ever, when you walk out on a job site, the contractor, their supervisors and foreman all have tablets, and information is being sent over from the office directly to them in the field. It’s much more real-time kind of access to things on a project”, he adds.
Poston also points to a growing trend in modularization, where large portions of a structure are built offsite and brought in to be installed.
Currently, modular construction accounts for only 5% of all commercial construction in the U.S., according to the Modular Building Institute, but it is growing. McKinsey & Co. estimates the market value for modular in new real estate construction could reach $130 billion in Europe and the U.S. in the next decade.