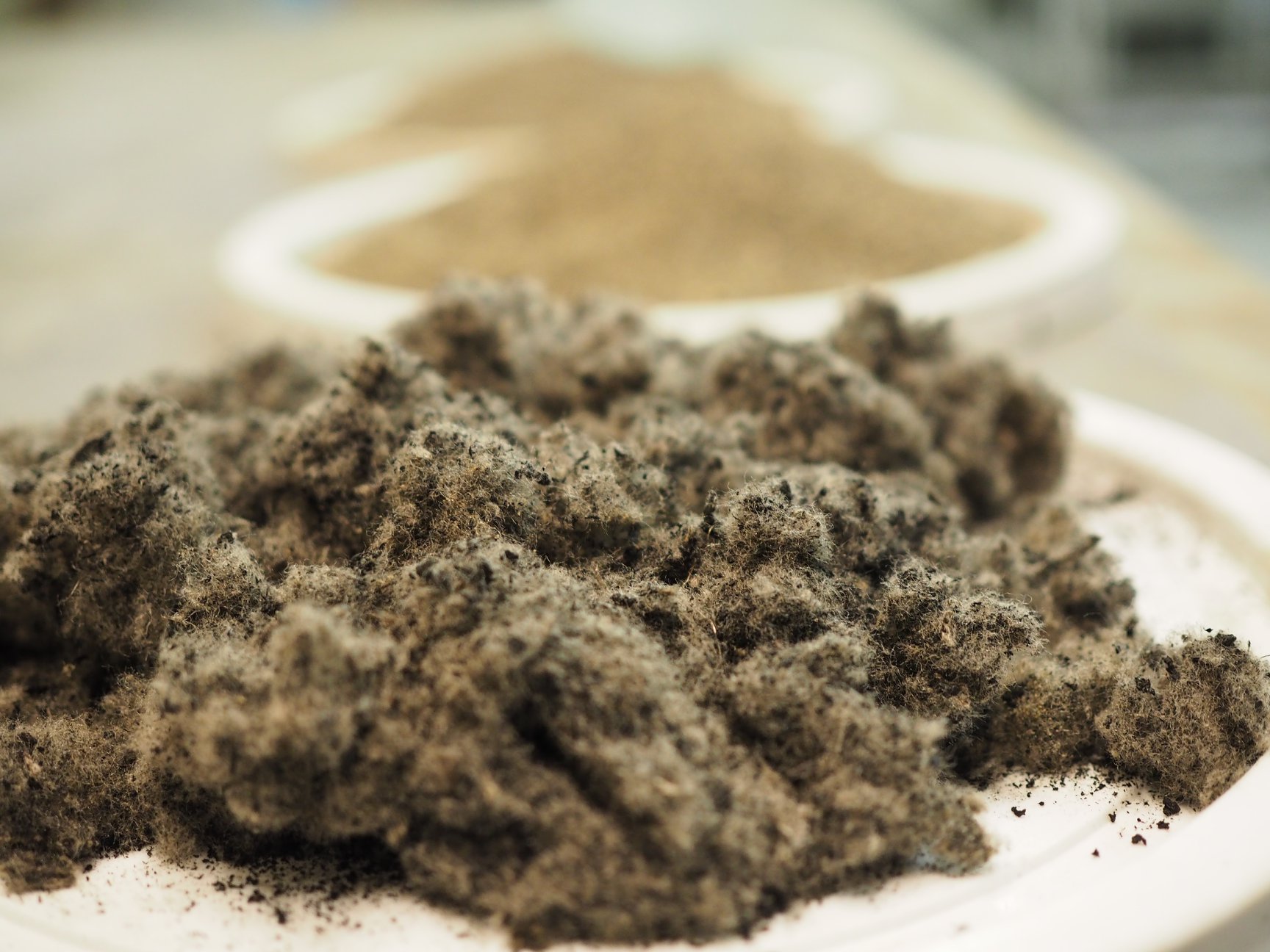
Polymer Fiber and STF — one of the byproducts derived from the processing of used vehicle tires. Presently, significant quantities of STF are generated annually in most developed countries of the world. However, traditional STF has been an amalgam of crumb rubber, steel and other particles, and its reusability has been limited… until now.
AtlantisFiber™ has developed Polymeric Scrap Tire Fibers (PSTF), which is an extracted blend of cleaned and refined fibers sourced from the recycled breakdown of tires. This proprietary blend has been specifically developed to be used globally in all types of concrete blends and uses. This technology has shown significant success in mild to extreme climates by forming a self-healing bond with the structure of the concrete, allowing load-bearing sections to possess enhanced structural integrity and reduced cracking by 90%.
Our Proprietary Polymer Fiber Blend
Vehicle tires contain different types of synthetic fibers such as nylon, polyester, rayon, and other materials, and tests were performed to determine the primary organic composition. From this, we have been able to develop an extracted blend of polymer-firer that is lightweight and economical, while providing an ecological benefit as well.
“It is well known that concrete is a quasi-brittle material with a low strain capacity. The randomly distributed fiber reinforcement can improve concrete brittleness, cracking resistance, toughness and ductility. Fiber-reinforced concrete (FRC) exhibits better performance not only under static and quasi-statically applied loads but also under fatigue and impact loads. This high energy-absorption attribute of FRC is often called ‘toughness’.” ~ Pat McConnell – President & CEO of AtlantisFiber™
What Our Case Studies and Real-World Applications Are Showing
Visual inspection of specimens indicates that the addition of fibers to mortar mixtures reduced plastic shrinkage cracking significantly. Compared to the large transverse through cracks observed in the reference specimens, fiber-reinforced specimens seem to have small-sized and segmented multiple cracks, however, none of the specimens containing fibers had cracks that were wider than 0.7 mm.
Moreover, while the reductions in maximum crack width in comparison to the reference mortar ranged from 86.4% to 93.2% for specimens containing fibers, the reductions in maximum crack indicate that both fibers were very effective in reducing plastic shrinkage cracking. Compared to the reference specimens, the addition of our final polymer-blend varied from 96% to 99.4%.
For more info, you can read and watch videos on our process here or download our “Durability performance of polymeric scrap tire fibers and its reinforced cement mortar” Abstract. If you interested in connecting further, contact AtlantisFiber™here or alternatively, we are on LinkedIn and would love to connect with you there!