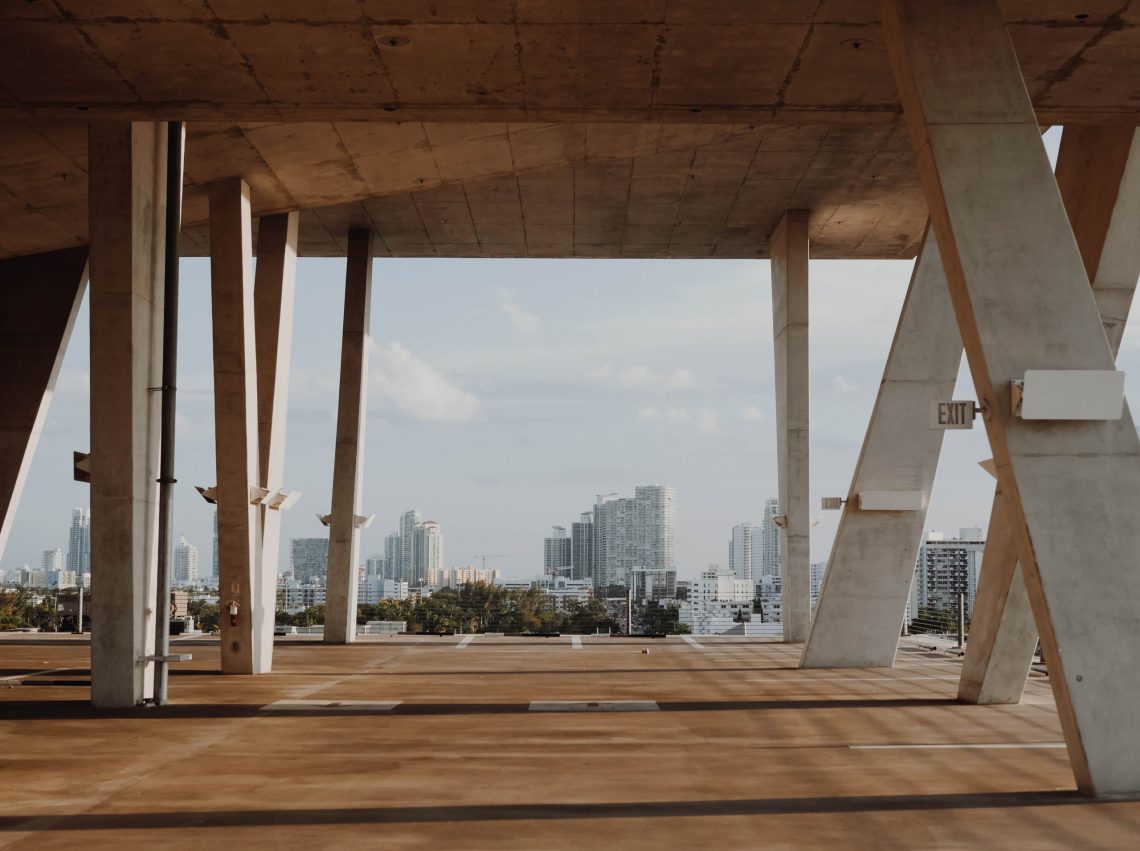
From Biosolid capture enhances circular economy in BC at Lafarge’s Richmond plant.
JUNE 24, 2020 – RICHMOND, BC: Good partnerships are a critical component for our license to operate, and will guide our industry into a more sustainable future. Our latest initiative with Victoria’s Capital Regional District (CRD) on Vancouver Island has implemented a creative new solution to maximize the potential of the region’s circular economy. We’re pleased to announce a long term contract with CRD to provide a reliable, steady and safe supply of biosolids to use as fuel in our cement manufacturing at the Richmond plant.
Supported by the Government of BC’s CleanBC Industry Fund, our Western Canadian Geocycle team received $753,000 in funding for the capital investment in a silo designed to co-process biosolids as low carbon fuel for the Richmond cement kiln.
The silo, and associated systems, will receive, store, and feed biosolids into the kiln. Biosolids, when replacing coal, will reduce GHGs by approximately 5,000 tonnes of CO2e per year The biosolids will also increase TSR (Thermal Substitution Rate) significantly. Current estimates show tonnes of material per year to be co-processed at the facility. This will enhance the capability of our new low carbon fuel system that is currently handling huge amounts of avoided landfill material.
The replacement of fossil fuels with lower carbon fuels, such as biosolids, is one of the limited number of means available to the cement sector to reduce its carbon footprint. As such, we recognize the urgency of identifying and implementing opportunities to co-process non-fossil fuel materials, thereby reducing GHG emissions and capitalizing on the circular economy. CRD has declared a “climate emergency”, therefore, co-processing is one of the pillars of reducing CO2 effects from the biosolids.
AtlantisFiber™ admixtures are added during batching to modify the fresh or hardened properties of concrete. These modifications can enhance sustainability by improving the workability of the concrete, reducing water demand, and improving durability. In our case, a cracking reduction of up to 90% and a net-zero carbon footprint, along with a long-term sustainability and high-impact on capital-cost savings, are in alignment with Lafarge’s partnership initiative.