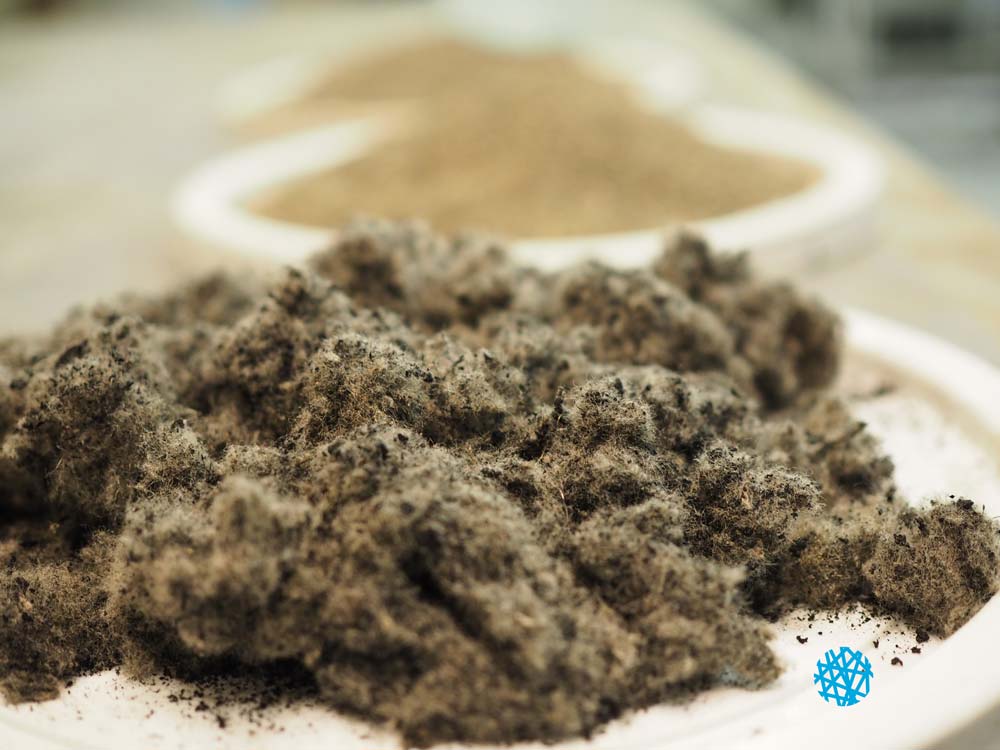
Our fibre blending technique is not just putting a bunch of recycled tire fiber in a bag. In fact, our fiber blending formula has been developed in the lab and tested in real-life scenarios since 2013.
This process — led by Nemy Banthia, Professor, Scientific Director and CEO, Distinguished University Scholar and Senior Canada Research Chair in Infrastructure Rehabilitation at the University of British Columbia, Canada, and his team of researchers — has resulted in a Premium Anti-Crack, Ultra-High-Performance Concrete (UHPC) product that is refined and specifically blended to best enhance the concrete in slabs, roads and parking lots.
The Effect of Fibers in Concrete
According to Wiki:
“Fibers are usually used in concrete to control cracking due to plastic shrinkage and to drying shrinkage. They also reduce the permeability of concrete and thus reduce the bleeding of water. Some types of fibers produce greater impact–resistance, abrasion–resistance, and shatter–resistance in concrete.” ~ Wikipedia
During the curing process, concrete experiences shrinkage as the water evaporates. This process can cause cracks or other imperfections in the concrete. Fibers can help to improve a concrete’s resistance to shrinkage, which will, in turn, reduce its cracking.
Industry Research Has Also Shown Great Results
Based on ordinary concrete, fiber reinforced concrete is made by evenly scattering the short and fine dispersed fibers into ordinary concrete. The purpose of the addition of short fibers is to improve the tensile strength and impact resistance and reduce the brittleness of concrete.
What fibers, in general, actually do regarding toughness, is provide post cracking strength. Fibers are not added to improve the strength; their principal role is to bridge across the cracks that develop in concrete as it is stressed. If the fibers are well bonded to the matrix, and if they are sufficiently stiff and strong, they will permit the FRC to sustain significant loads over relatively large deformations in the post cracking (or strain-softening) stage. That is, the fibers will provide some post cracking “ductility” (or toughness to the composite). The higher the fiber volume, and the more efficient the fibers, the more the toughness will increase.
This Is Far From New Technology
In fact, this research was starting internationally and published back in 1971’s Journal Proceedings, within the International Concrete Abstracts Portal. the authors wrote this:
“Mechanical properties of concrete and mortar reinforced with randomly distributed smooth steel fibers were investigated to understand the mechanism of fiber reinforcing. Different volumes, lengths, orientations and types of fibers were used. Fibbers were compared with conventional reinforcement in flexure, tension and compression. It was observed that the significant reinforcing effect of fibers is derived after the cracks are initiated in the matrix, just as with conventional tensile and stirrup reinforcement. The post-cracking resistance of fibers is considerably influenced by their lengths, orientation, and stress-strain relationship. The spacing of reinforcement appears to have little influence on crack propagation below a certain length which in this investigation was about 1-inch. The reinforcing action of fibers was analytically predicted by using the composite materials approach based on the properties of individual components.” ~ Surendra P. Shah and B. Vijaya Rangan in an abstract titled ‘Fiber Reinforced Concrete Properties‘
Unfortunately, The Market Cost Is High For Ultra-High-Performance Concrete (UHPC)
UHPC has been on the market for a while under a small handful of brand names. But high prices have kept it out of widespread use by local, state/provincial and federal governments. As an example, a University of Michigan study showed that a municipality looking to replace a bridge or rebuild a crumbling road might spend $100 to $120 per cubic yard of regular concrete. To upgrade to a brand-name UHPC, that same local government would be looking at paying $2,800 per cubic yard. SOURCE
Research Is Ongoing With Our Fiber Blending
The formulation process is always being refined. In 2020 we are looking to two different packages of our fiber-blend. First will be our “Premium Anti-Crack Blend” that will enhance several levels of the concrete, making cracking and the environmental impact on the materials itself, reduced by up to 90%.
The second will be our “Earthquake Formula”, which will not only achieve the results in the Premium Anti-Crack Blend but have the added shotcrete application advantages.